The supply chain has been under intense scrutiny for as long as humankind has exchanged goods. At some point, the phrase "What do you mean, you don't have any beaver pelts available to trade?" was probably uttered.
That scrutiny peaked during the pandemic as manufacturing facilities, distribution centers, and warehouses shut down, cut staff, or fell behind. Demand for direct-to-consumer shipping grew to proportions that have become a new norm. Ongoing labor issues have operators looking for new ways to do more with less.
As resellers continue to comb for opportunities, it is important to determine where warehousing, logistics, and distribution professionals stand with technology in their daily business. Where are they most frequently encountering errors in their processes? What kind of mobile hardware do they use each day? How do they handle IT tasks? What emerging tech are they expecting to bring into their world soon? Some results are eye-opening, some will reinforce what we already think, and all should inform your business planning for the rest of the year and beyond.
Special thanks to Zebra Technologies for sponsoring this survey and helping us determine the questions.
The Methodology
We worked with a third-party data collection company for this one. They made 1,750 calls to get 98 responses to a survey we provided. That survey was 45 questions designed to learn about the respondent's industry experience, their daily pain points, and a deep dive into the hardware and systems they deploy to manage their business with an emphasis on mobile devices like handheld computers, barcode scanners, and RFID readers.
Respondent Businesses by Type
Roughly two-thirds of those surveyed had 5-10 years of experience in their current industry and the remaining majority at 10-20 years. Company size was well distributed, but over half have between 100-500 employees globally.
Job Experience Breakdown
Job Seniority Breakdown
Our Findings
Pain Points
We started the survey by asking some "current situation" questions to uncover pain points, business operations, and existing technology usage.
How often do you experience errors in each of the following?
Very Often | Somewhat Often | Not Often at All | |
Receiving Errors | 31% | 68% | 1% |
Putaway Errors | 46% | 64% | 0% |
Picking Errors | 27% | 60% | 3% |
Packing Errors | 32% | 66% | 2% |
Shipping Errors | 47% | 52% | 1% |
Inventory Errors | 64% | 45% | 1% |
Return Errors | 14% | 64% | 22% |
Errors happen in most businesses, but some happen more in warehousing. Inventory was the clear leader here, followed by shipping and putaway. Few indicated that errors were rare, with returns being an exception, likely due to a follow-up question that revealed that only 18% of respondents handled reverse logistics. We asked that 18% an additional question.
In your opinion, what technology or other process improvements would simplify or otherwise improve your reverse logistics?
Here's a representative sample of responses:
- "Improving communication and coordination between suppliers, manufacturers, and retailers"
- "Better return policies"
- "RFID and barcode scanning technology for better tracking and identification of products that can handle inventory management simultaneously"
- "Simplifying the process by using predictive management software to reduce downtime and improve operational efficiency"
Mobile Technology in Use
Next, we wanted to learn more about the technology currently in use. 98% of operators used mobile devices (tablets or handheld computers). 95% said such devices are essential to logistics operations, and only 11% said they used consumer-grade devices (primarily for communication).
Do you use devices that could be considered consumer-grade in non-office areas of your business?
What barcode & mobile computing brands are in use in your facility?
Out of the collected responses, Zebra Technologies was the most recognized brand. We've omitted the other brands mentioned as part of this study. In the interest of transparency, Zebra was the funding sponsor of this study. However, this was not identified to the survey respondents, nor were the respondents prompted with Zebra or any other brand names.
What barcode or RFID reading devices do you use in your warehouse operations?
ALL operators we surveyed use handheld barcode scanners, and most use RFID scanners & rugged computers with scanning capabilities. Over half used fixed RFID, but only a few had implemented hands-free scanners.
That RFID usage was further verified when all but one person indicated they used RFID technology in their business, with 95% of them saying they do so daily! Given how much we discuss the potential of RFID in the reseller channel, warehouse and logistics are bought in already.
On a scale of 1-10, with one being "Very Unsatisfied" and 10 being "Very Satisfied," how happy are you with your mobile computing devices such as tablets, scanners, or mobile computers?
Only 13 answers indicated a satisfaction level below 7, and no one said less than 5. That's a good sign of brand loyalty and the reliability of purpose-built devices.
We asked about handheld devices using a Windows OS. 100% said some of their devices did, with the majority (89%) saying at least half their mobile hardware was running Windows.
On average, how many different computing devices (such as rugged handhelds or tablets) or communication devices (headsets, phones, Two-way radios) does a single associate use during a shift?
Most warehouse workers are using two or three computing or communication devices daily. That also inspired us to ask about mobile device management (MDM). All but one said they use an MDM platform to locate devices, install software, or manage security. 63% of respondents were still using two-way radios to communicate from the floor of their facility, and the rest were using software on their handhelds.
How often do you experience issues with your barcode scanners?
A quarter of barcode scanners (26 responses) are experiencing occasional issues. We also asked what the most common issues were. Speed-related problems topped the list, with breaking or glitches related to rugged conditions coming in second.
Other Technology Insights
We wrapped up the survey by learning more about each respondent's overall technology environment, including systems in place, IT management, and the emerging tech they're most interested in.
Almost 100% of operators used a TMS, WMS, and ERP, so we inquired about their IT team. 82% said they have an in-house IT department, while 51% indicated they either exclusively used or supplemented with an outside IT organization.
About how many members are part of your global IT team? (In-house)
Most warehouse and logistics companies have more than ten IT team members, but usually not more than 50.
We also wanted to know more about in-house and external IT team responsibilities. Here are the top five responses for both:
There's not much crossover there, and operators look outside their teams to address cybersecurity, software needs, and hardware repairs.
What is your process when it's time to replace warehouse tech hardware?
Candidly, the responses here left a bit to be desired in terms of usefulness or depth, but here is a representative sampling of answers to this open-response question:
- Identifying issues, needs the hardware should address, and standards like cost, durability, and features
- Look for the best replacement option on the market after evaluating the condition of current devices
- Test hardware in a controlled environment
- Establish a budget for replacements, along with a timeline and process for implementation
- Obtain quotes and installation timelines from vendors
- Discuss needs and requirements with the IT team
- "Define the hardware requirements for the new devices based on the business needs of the warehouse"
That last quote was a common refrain, as meeting the business's specific needs is top of mind for most operators. It was also notable that very few responses indicated collaborating with outside partners or suppliers early in the process, instead suggesting that once much internal diligence and discussion had occurred, potential or preferred suppliers would be contacted.
How are you sourcing your media supplies (printer supplies, labels, etc.)?
Over half of the respondents manage media/supplies ordering internally. A further question revealed that 75% would be open to exploring automatic re-ordering of these products.
Finally, we asked these key decision-makers where they expected to see technology investment in the coming years.
Which emerging technologies do you foresee investing in in the next five years?
Robotics/automation & AI platforms stood above the rest here. Half of the operators indicated that investment in WMS and RFID may be on the agenda despite near-universal usage established in earlier questions.
Key Takeaways
A shift in age and experience among warehouse & logistics leaders seems to have coincided with more technology adoption and acceptance. Here are the responses that stood out to us and what they may mean to VARs, ISVs, and vendors working with this industry.
RFID is Table-Stakes - A long-running gag in our channel has asked, "Is this the Year of RFID?" This survey would indicate that for warehouses & distribution centers, it's simply part of the daily operations. Only one respondent wasn't using RFID and, when asked why, responded that it was the "complexity." If you encounter such a hold-out, remind them that they are behind the times (in a nice way) and offer to help them overcome any hurdles to adoption.
Inventory Management Still Offers Opportunity - 64% of those surveyed said that inventory errors happened "very often," which presents an area for us to make a difference. Do some digging, discover what errors are occurring, and position solutions (especially with inventory-focused software partners) that can alleviate those issues.
The Android Transition is Slow-Going - None of these companies have completely moved away from Windows on at least some of their devices. While the benefits of Android (especially for MDM, security, and software integration) are apparent, and Microsoft is sunsetting its support, there is still work to be done, which positions us to be there when the inevitable transition occurs. Keep talking the Android talk, but don't snub the Windows users, who may need your support more than ever.
Advise and Communicate Early and Often - IT decisions and discussions in this industry are happening whether you are there or not. We've learned that B2B buying groups are, on average, 57% of the way through the purchasing process before they even contact a supplier. (Check out this episode of The TEConnect Podcast for more on that data and what it means.) The responses to how supply chain operators choose and replace hardware confirms that, making it imperative that you are seen as a trusted partner who wants to help and advise, even if there's no immediate sale. A consultative approach, designed to learn more about their business and find "champions" within who can speak on your behalf, is a useful strategy for having a seat at the table for those discussions, even if it's not a literal seat.
Get That Recurring Revenue - Media and supplies are gifts that can keep giving to a VAR. With 75% of our respondents open to automating their reorder process for printer supplies, there's an easy opportunity to lock yourself into ongoing orders.
Examine Your Portfolio - Warehouse & logistics companies seek external cybersecurity, software, and hardware repair assistance. They're looking at future investments in automation, robotics, and AI. Are those solutions part of your current stack, or do you have partner-assisted relationships in place that do? If not, now is to time to add them. If you need partners, BlueStar is here for you. Our TEConnect program gives us access to hundreds of software companies eager to work with hardware partners. We're routinely working with emerging tech companies to prepare for the next wave of innovation. You don't have to be first, but you don't want to be last.
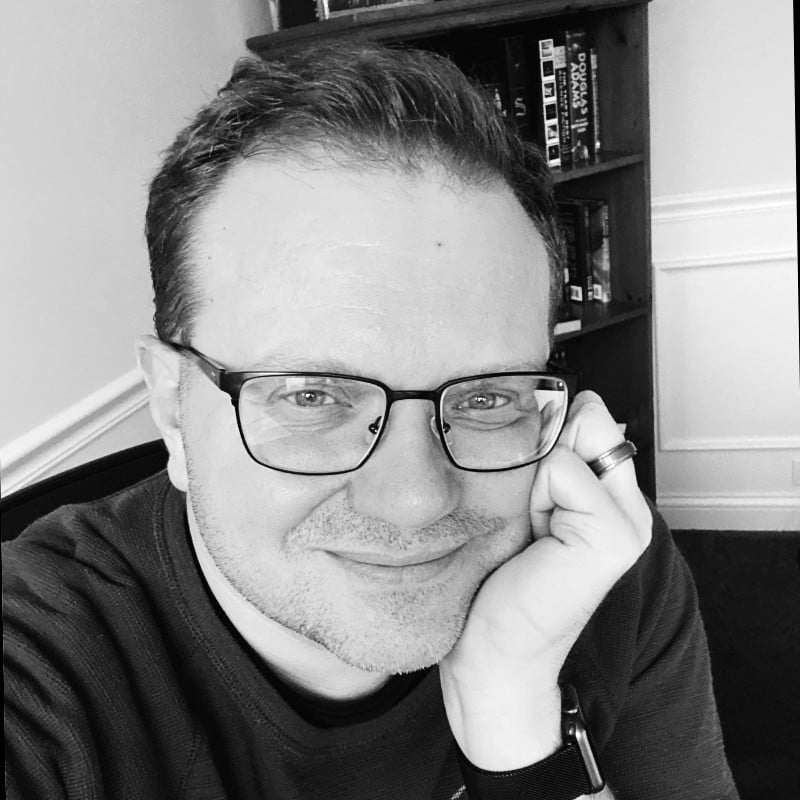