Speaking directly with 36 warehouse managers—the folks truly in the trenches of what's happening on the shop floor—would cost a VAR organization a plane ticket, a couple of nights at a Vegas hotel, a handful of meals, and a trade show ticket.
Let's call it $1,900, conservatively. Instead, we thought we'd save you the trouble and talk to them for you.

We ran a Facebook ad that targeted warehouse managers, offering them a $15 amazon gift card to complete our survey. Survey respondents were walked through a series of 5 questions by a chatbot. At the end of the survey, we provided them with a link to redeem their gift card. All respondents were based in the United States, as confirmed by their IP addresses.
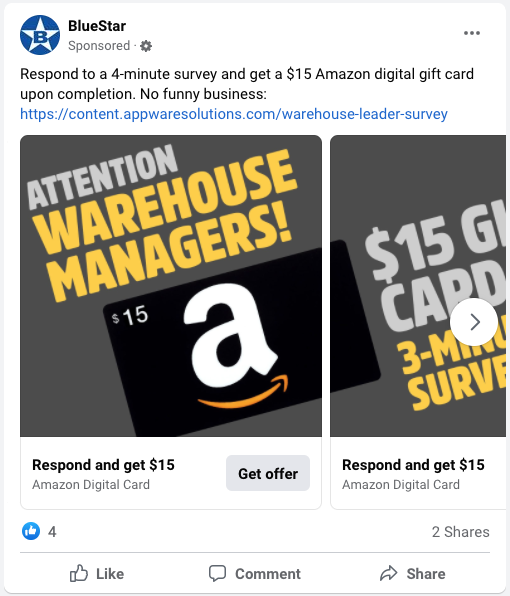

Amongst the survey respondents were warehouse managers in industries such as furniture rental, medical supplies, beauty/fashion, produce, fulfillment centers, art supplies, child care products, breweries, logistics, wholesale flooring, and more.
Survey respondents represented many regions of the country, with some small pockets in New England, Florida, and Southern California.
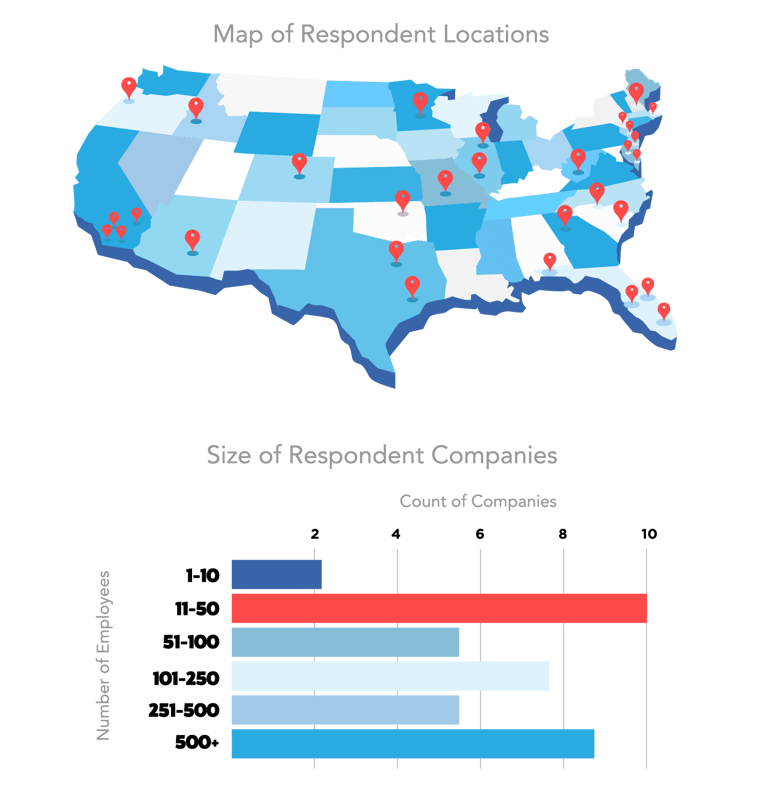

When we posed the question:
Which of the following is the biggest problem area in your warehouse?
(Choices Included: Inventory/Cycle Counts, Receiving, Putaway, Picking, Packing/Shipping)
The majority of respondents (18) indicated that Inventory / Cycle Counting was the biggest problem area. However, 25 out of 36 overall responses and 10 of 18 who identified inventory as the biggest problem area indicated that they were already using either handheld or fork truck computers. So, we dug a bit deeper into the open field responses to "What specifically is it about this problem area that is the issue?" while considering sizes of organizations—and this is where we uncovered the gold.
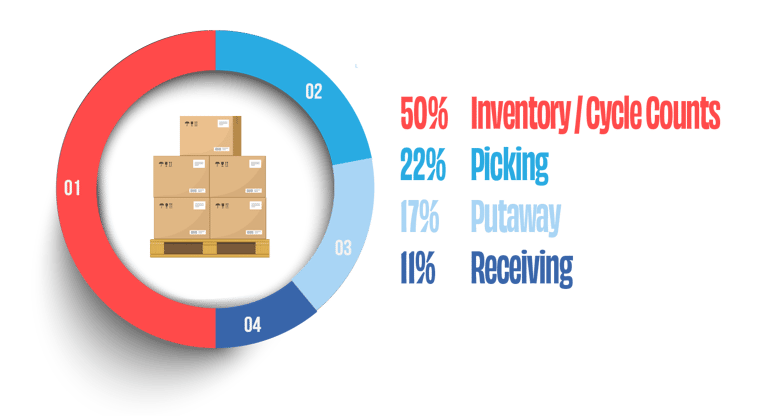
The main contributors to inaccurate and otherwise imperfect inventory systems included:
- No inventory software system in place (small organization)
- Too much inventory on hand; storing in multiple locations (large organization)
- High number of SKUs to count (medium-sized organizations)
- Mismatched data in physical count vs system (multiple responses and org. sizes)
- Heavy time commitment to do regular counts (multiple responses and org. sizes)
- Materials and items are not where they're supposed to be—associates moving things without updating the system (large organizations)
"The inventory software is difficult to learn. Only a few people in the warehouse know how to use it."
OPPORTUNITY:
There is seemingly a clear need for ongoing technical training for warehouse associates. In response, VAR and ISV organizations could offer regular virtual or in-person training programs that could present a recurring revenue stream. The reality that regular inventory counts are time-consuming isn't surprising but points to the continued potential for cost-effective RFID solutions.
Chris Jackson from Savant Software on training warehouse teams:
However, not all of the headaches were associated with inventory management—22% of the surveyed managers (6) said that Picking was their biggest problem area. This was almost exclusively an issue for larger organizations, half of which indicated that they did not have a WMS in place.
Next, we asked:
What is the #1 technology-related issue in your warehouse?
(OPEN FIELD)
Unsurprisingly, several of the answers echoed the earlier response about Inventory Management being a problem area—answers included sentiments such as "inventory software is a joke," to "everything relies on paper with little tech used." But even for those who mentioned inventory as being the biggest problem area, a top response to the #1 tech issue question (7) was about dropped zones and unreliable wireless connectivity throughout the space.
A respondent from a large retail chain in the art and hobby supplies industry wrote,
"Our network has problems. When it's down, you spend time trying to fix it and get behind on your tasks."
The main culprits:
- flawed WMS implementations ("WMS not synced with actual inventory")
- non-purpose-built solutions ("we're using a production system for inventory")
- dropped zones / unreliable wireless connectivity
- old/outdated systems that lacked functionality
- incomplete or difficult to scale training ("only a few people know how to use the system")
- complicated processes and sophisticated software systems
- human error due to incomplete or inadequate training
"...our #1 technology issue is getting users to properly operate within the inventory system's parameters. In most cases, if the input is correct and accurate it all works out."

At at end of the road, we let folks do a little dreaming when we asked:
If money wasn’t an issue, what new technology would you most like to implement or upgrade in your facility?
(OPEN FIELD)
Here is what was on their wish lists:
- Warehouse Management Software and related applications (16)
- Upgraded WLAN / WiFi / "Internet" or "Connectivity" (6)
- Barcode Scanners (6)
- RFID / RF Scanners (5)
- Forklifts (4)
- Robots (2)
- Dimensioning Systems (1)
- Mail Tube System (1)

- Many smaller businesses don't have the hardware tools (scanners, mobile computers, tablets) necessary to effectively manage inventory
- WMS / inventory management systems have flawed implementations, training is incomplete and/or tough to roll out for new associates, or is complex to learn
- The wrong tools are being used—legacy systems that lack modern functionality, production (non-WMS) systems, POS modules, and more.
- User error is common in physical (receiving, putaway, picking) processes as well as in software system use
- Putaway is plagued by excess ordering, lack of space, staff shortages, and general disorganization.
Justin Griffith from StayLinked on the importance of usability in warehouse software:
If you found this article interesting, stay tuned. We plan to survey end customers across a variety of industries to gain insights into problem areas and attitudes towards existing technologies to help identify areas of opportunity for value-added resellers and software vendors.